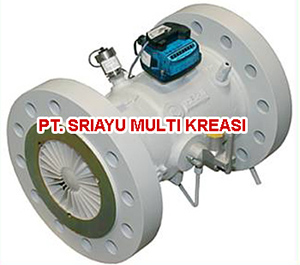
ITRON G65 Fluxi 2000 are are flow meters. The flow of gas turns a turbine wheel, and thus, the rotating speed of the turbine is proportional to the linear speed of the gas.
The movement is mechanically transmitted to the totalizer through the magnetic coupling.
Description :
The Fluxi 2000/TZ meter is composed of five main parts :
- A body containing all the components
- A flow straightener to stabilize and accelerate the gas flow before the turbine wheel
- A measuring unit including the turbine wheel
- A magnetic coupling to transmit the movement of the turbine wheel to the totalizer
- A totalizer to register the measured gas
Applcations :
Fluxi 2000/TZ meters are designed to measure natural gas, and various filtered, and non-corrosive gases. They are used to measure medium to high gas flow, ta low, medium or high pressure.
Fluxi 2000/TZ have been optimized for use in all application related to the transportation and distribution of gas. Fluxi 2000/TZ meters are approved for fiscal use.
Technical Specifications
Metrological Approvals :
- Compliant with the Measuring Instrument Directive 2004/22/EC
- Approval number: DE-10-MI002-PTB001
Intrinsic Safety Approval :
- Compliant with the Directive 94/9/EC
- Approval number: LCIE 06 ATEX 6031 X
Flow Rate : From 5 m3/h to 10000 m3/h, G65 to G6500.
Nominal Diameters : From DN50 to DN400 mm (2” to 16”).
Maximum Working Pressure : Up to 100 bar depending on the body material and flanging.
Mounting : The Fluxi 2000/TZ meters can be installed either horizontally or vertically, for the DN50 to DN300, and horizontally for the DN400
Body Materials :
- Ductile iron, cast steel or welded steel
- Compliant with the Pressure Equipment Directive 97/23/EC
Temperature Range :
- ATEX/PED: -30°C to +60°C
- MID : -25°C to +55°C
- Storage temperature : -40°C to +70°C
Totalizer:
- 9-digit index to register a larger volume
- 45° orientation for an easy reading
- Free-rotating totalizer
- Equipped as standard with the cyble target: it allows the installation of the cyble sensor at any time.
- Equipped with 1 built-in silicagel cartridge; as an option, equipped with an external cartridge to enable easy maintenance even in extreme conditions
- Fitted with a reflecting disc on the first drum.
- Integrated optical disc to facilitate the periodic calibration of the meter.
- Customized name plate (logo, bar-code, customer serial number…)
- IP67 protection
- UV resistant
- Unit: m3
Transmitters
- Cyble sensor: It can be delivered mounted onto the meter or installed afterwards at any time. The Cyble sensor is a bounce-free transmitter. It allows also the counting of eventual back flows.
- Low Frequency (LF): Two Reed switches are fitted as standard on the whole range. Anti-tampering (AT): this device is fitted as standard on the whole range.
- Medium Frequency (MF): one transmitter is supplied as an option.
- High Frequency (HF): up to 4 transmitters are supplied as an option on the whole range.
- Mechanical drive: the totalizer can be fitted with this option, it may be used to drive removable accessories. The mechanical drive is designed according to EN 12261.
Oil pump
- An oil pump is supplied as an option, which lubricates the main ball bearings in the measuring unit. The oiling can be done even when the meter is under pressure.
Turbine wheel
- This is the most important component of the meter for achieving high accuracy
at low and high pressure. It can be made from aluminium for the whole
range or in polyacetal for the DN≤200. Depending of the G size, the blades of the turbine wheel are oriented at 45° or 60°. Turbine wheel at 60° is used to avoid over-speed of the wheel. When a HF3 is requested, the wheel must be in aluminium. For high pressure use, or for measuring dirty gases, an aluminium wheel is recommended.
Flow Straightener
- This device stabilishes and accelerates the flow before the turbine wheel. It has been designed to meet the requirements of the 2 perturbation tests defined in the EN12261 (low level and high level perturbation).
All DN meet the requirements of the low level perturbation test without an additional device with only 2 DN inlet straight pipe, 0 DN outlet of the meter.
From DN50 to DN150, no additional device is required to fulfil the high level perturbation test with only 2 DN inlet, 0 DN outlet of the meter.
From DN200 to DN400, a flow conditioner has to be integrated in the inlet of the flow straightener to meet the requirements of the high level perturbation test when only 2 DN inlet pipe is available (see in § Accessories).
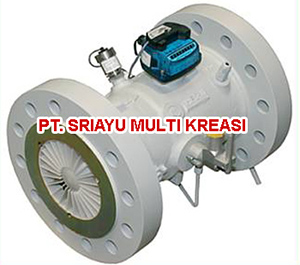